BRIEF OVERVIEW
It was during the earliest times of lock down, think3D was declared operational under the essential services act by Govt of India, due to our presence in the medical device manufacturing zone. Although it was the moment of sheer panic all over the country, we felt proud to serve in those trying times. We have kept our facility operational all through to develop various need-of-the hour products like face shields, ventilator splitters, ventilators, COVID-19 machined components and COVID-19 test kits. Amid the great crisis, many medical companies have approached us to either give shape to our innovative ideas or scale up their production to cater to the demand. MOLBIO Diagnostics Pvt Ltd is one such company that has availed our services to manufacture COVID-19 test devices in big numbers.
PROBLEM STATEMENT
Our client has approached us with the following challenges to solve,
- They are running out of time to meet the sudden demand of COVID 19 test kits.
- The components are very intricate & tiny and thus require high precision manufacturing expertise.
- Cutting edge machining devices in big numbers are required to manufacture the parts in a limited period of time.
OUR SOLUTION
While think3D is equipped with CNC machines and have the competency to manufacture the parts, bulk quantity required & short timelines forced think3D look for collaborators to take up the project. think3D partnered with various Governmental tool rooms like CTTC, IGTR to augment the capacity. In the midst of lock down, think3D alongside our partner network arranged the required transport and permissions to get the team and raw material in the middle of the complete nation lock down.
From the diagrams provided by the client company, we did a detailed process planning using our in-depth understanding of machines, technologies & materials to optimize the resource utilization, plan for multi-shift program and arrange the required raw material. We delivered the entire 12,000+ parts in a matter of 3 months. The project otherwise would have taken more than 6 months to complete. These components were tooled, tested and sent to the client.
Data Provided By Client:
The drawings of the 21 components were given to us by the client company for reference and the same were shared to the team while manufacturing.
Machining Process:
Once the drawings were received, our designers converted them into 3D files (.stp) for better understanding. We chose CNC Turning-Milling-EDM wire cut in respective order to manufacture the components. These parts have a tolerance of less than 20 microns. Once the machining is done, the parts had undergone post processing like threading, buffering, divering etc.,
Final Output:
Below are the final components/ parts of the COVID test kit device manufactured at think3D.
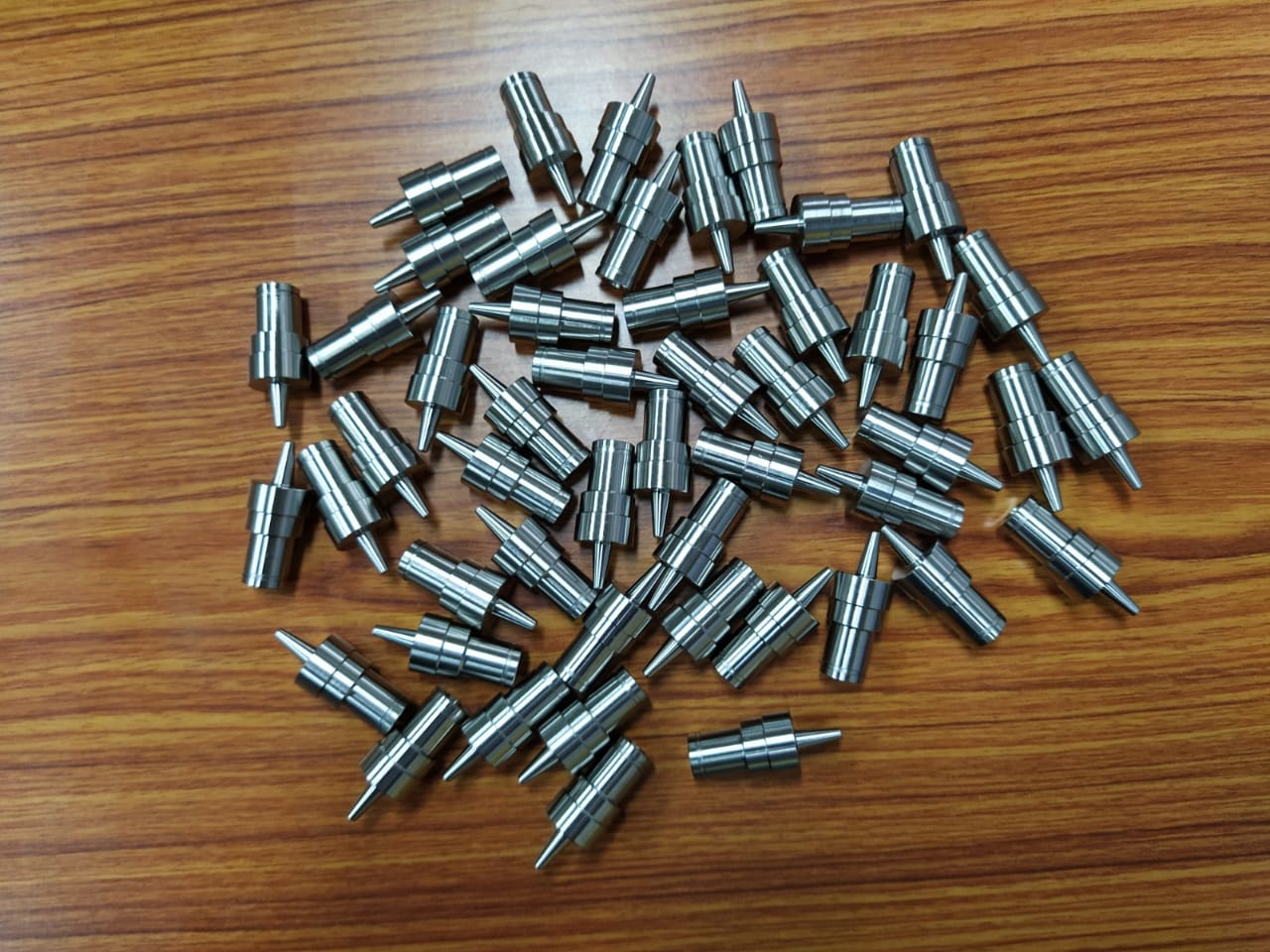
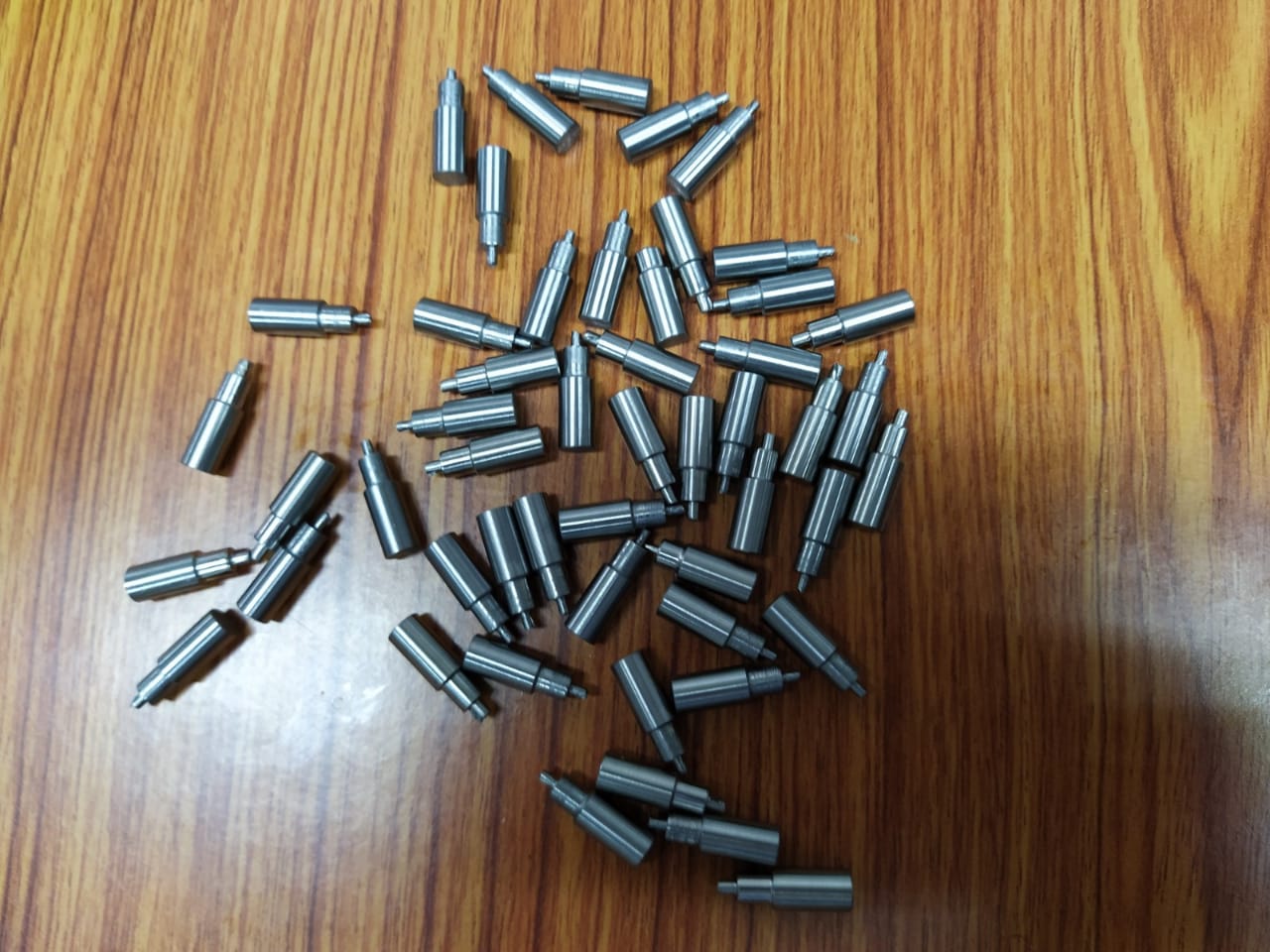
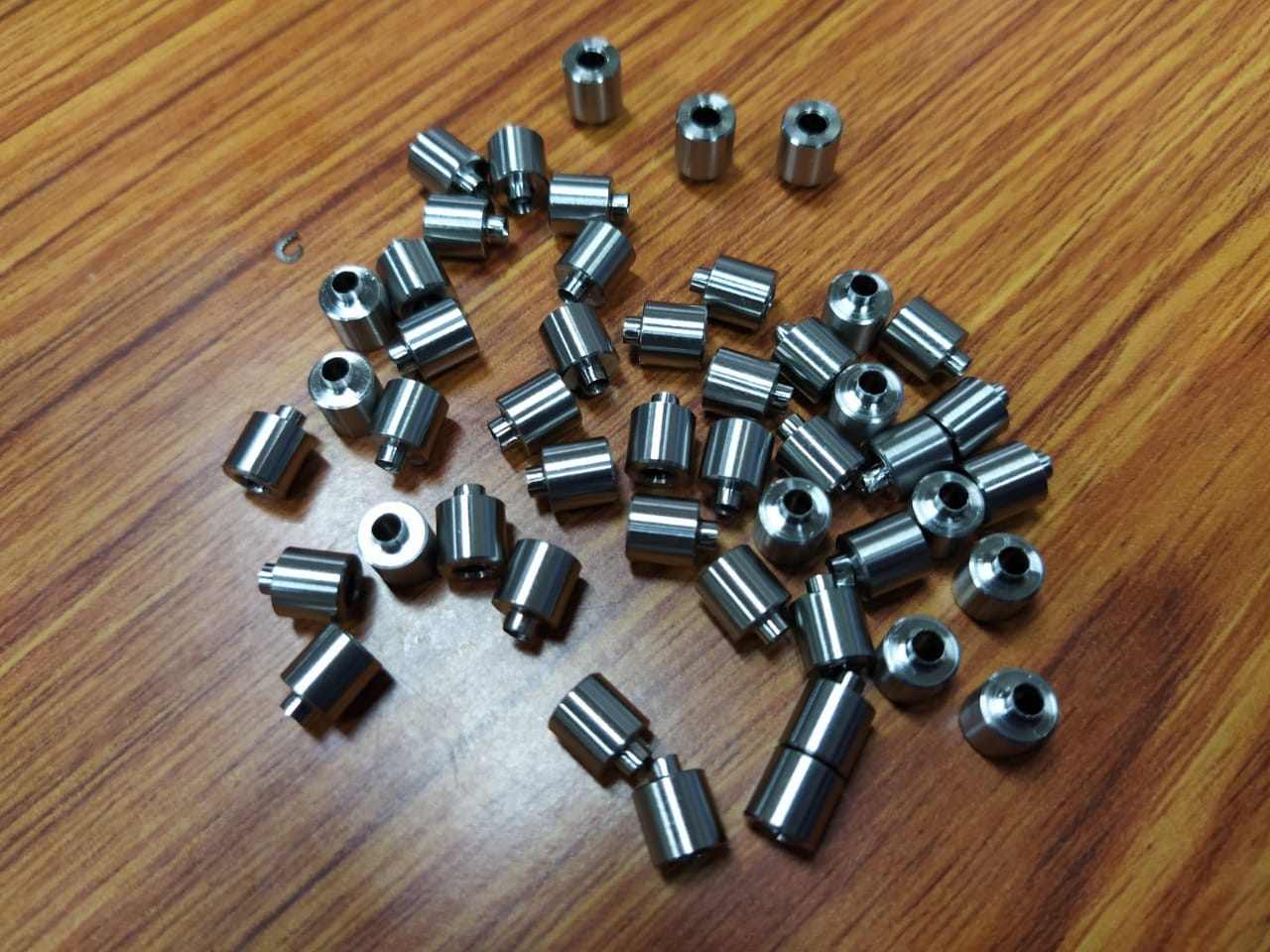
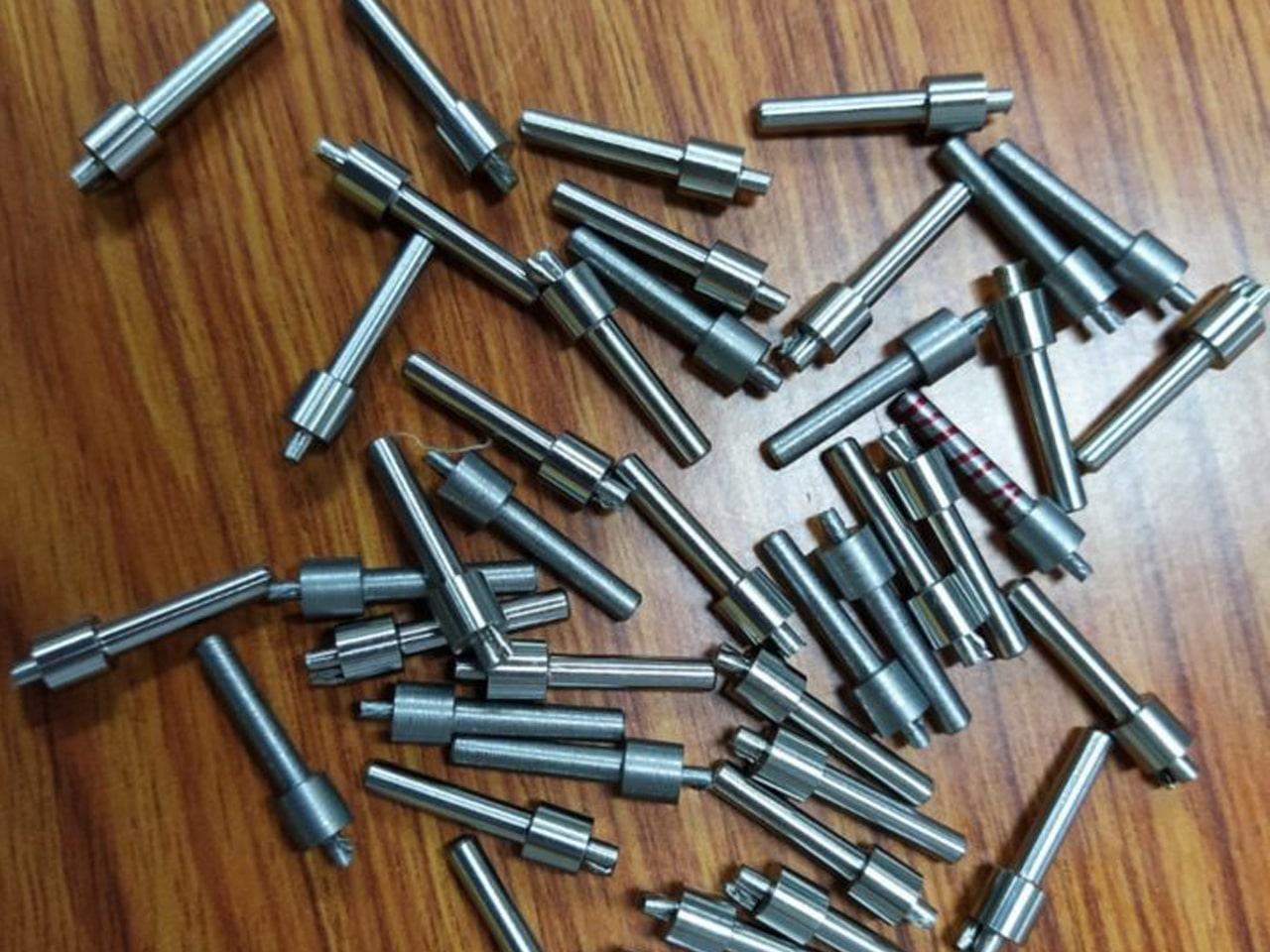