3D Printing is also called as additive manufacturing. It is a process of creating a 3-dimensional object from a CAD model by adding successive layers of the material. There are several different technologies in 3D Printing. In fact, all the technologies similar as they construct an object layer by layer to create complex shapes.
FUSED DEPOSITION MODELING
FDM is mostly used 3D Printing technology. FDM or Fused deposition modelling is a layer additive manufacturing process that uses production grade thermoplastic materials to produce both prototype and end-used parts. This technology is known to accurately produce feature details and has an excellent strength-to-weight ratio. FDM is used for concept models, functional prototypes manufacturing aids and low volume end used parts.
The FDM process begins by slicing 3D CAD data into layers, the data is then transferred to the machine which construct the part layer by layer on a build platform. Thin thread like spools and thermoplastic and support material are used to create each cross section of the part. Then the material is slowly extruded through dual heated nozzles precisely lay down both support and thermoplastic material upon the preceding layers, the extrusion nozzle continues to move in a horizontal XY plane while the build platform moves down then building the part layer by layer. The finished part removed from the build platform and cleaned of its support material.
Materials: ABS, Flexible, Nylon, PET, Wood, PLA, PC, HIPS

STEREOLITHOGRAPHY
Stereolithography or SLA is a rapid prototyping process used to create parts from 3D CAD data in a matter of hours. SLA is a highly accurate additive manufacturing process and may also be referred to as prototyping or 3D Printing. Models created with this technology are typically used as concept models, for form and fit studies, or as master patterns for molding techniques. The SLA process begins when CAD data is sliced into thin cross-section or layers, typically about six thousands of an inch thick.
This data is then transferred to an SLA additive manufacturing system containing a vat of UV-curable photopolymer. The machine begins to build the part one layer at a time. Each layer is constructed from a ultraviolet laser that is directed by X and Y scanning mirrors. As the laser traces the cross-section on the surface of the resin, the liquid material is hardened on contact. Once a layer is complete, the build platform is indexed down to make room for the next layer. A recoater blade moves across the surface ensuring a thin coat of fresh liquid resin is evenly spread over the object. The laser continues to trace and form each layer a top the previous layer, building from the bottom up. The completed part is then carefully removed from the liquid and separated from the platform. A chemical bath removes excess resin and the part is cured in an ultraviolet oven. Any support structures are also removed at this time.
Materials: Acura 25, Acura 60, Accura Xtreme, Accura Cast pro
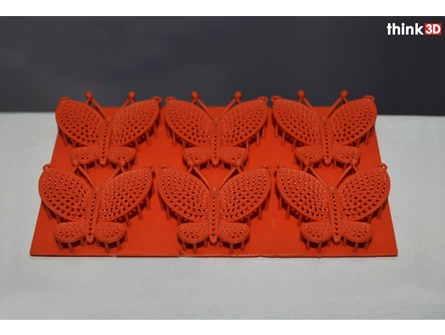
SELECTIVE LASER SINTERING
Selective Laser Sintering or SLS is a rapid prototyping technology that turns 3D CAD data into physical parts. SLS is an additive technology that uses powdered Nylon 12. Parts produced are light-weight, highly durable, and both heat and chemical resistant, making SLS an excellent choice for producing production parts without the expense of tooling.
The SLS process begins by splitting 3D CAD data into thin cross-sections or layers. The data is then transferred to the SLS additive manufacturing equipment. The machine then begins to create the first layer. After a leveling roller spreads a thin layer of powdered material across the powder bed, a CO2 laser traces the cross-section on the material. As the laser scans the surface, material is heated and fused together. Once a single layer is complete, the powder bed is lowered to make room for the next layer. More material is introduced from the powder catridge and rolled out smooth, while unused material is recycled. The process is repeated, building layer upon layer until the part is complete.
As SLS parts are built, they are encompassed by unsintered powder which provides supplemental strength and eliminates the need for support structures. Complex designs and assemblies once thought and impossible are now being redesigned with SLS at cost effective integrated structures solid concepts and new factures parts utilizing nylon with property enhancing filters to create rugged SLS parts suitable for a variety of protoype and production applications.
Materials: PA Nylon (for regular applications), Glass filled Nylon (for higher strength applications)
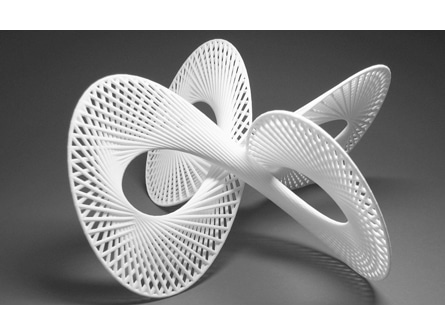
DIRECT METAL LASER SINTERING
Direct Metal Laser Sintering or DMLS is an additive manufacturing technology that create metal parts directly from 3D CAD data without the need of tooling. DMLS utilizes a variety of metal and alloy materials such as alluminium, maragining steel, cobalt chrome to create durable parts and prototypes. DMLS is an excellent choice for functional metal prototypes, high-temperature applications and end-use parts.
The DMLS process begins in the same fashion as other layer additive manufacturing technologies. A program takes 3D CAD data and mathematically slices it into 2D cross-sections each of these sections will act as a blue print telling the DMLS machine exactly where to center the metal material, the data is then transferred to the DMLS equipment. A recoder assembly pushes powdered metal material from the powder supply to create a uniform layer over the base plant. A laser then draws a 2D cross-section on the surface of the build material heating and fusing thematerial. Once a single layer is complete the base plate is lowered just enough to make room for the next layer more material is raised from the catridge and recoated evently on the previously centred layer.
The DMLS machine continues to center layer upon layer building from the bottom up as the part is built suppor structures are added to give supplemental strength to find features and overhanging surfaces. The completed part is then removed from the base layer and treated with an age hardening heat process to further harden the part. Any support structures are also removed at this time.
Materials: Maraging Steel MS1, Stainless Steel ss316, Cobalt Chrome cp1, Aluminium AlSi10Mg, Titanium ti64, Inconel (Nickel Alloy)
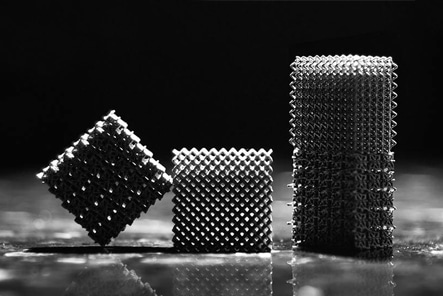
COLOR JET PRINTING
Color jetting or binder jetting 3d printing process can produce high-definition, full-color prototypes or early-stage concept models affordably. As models are 3D-printed directly in color, ColorJet allows you to analyze color variations at an early stage without having to spend the extra time and money for post-process painting.
The CJP process begins by splitting 3D CAD data into thin cross-sections or layers. The data is then transferred to the CJP additive manufacturing equipment. A roller mechanism spreads an even layer of white powder, the core material, across the build platform. The print heads then selectively jet the binder onto the powder to bind the subsequent layer of core material. The liquid binder serves the dual task of fusing the layers and coloring the part in a multitude of shades. As is the case with other powder bed systems, once a layer is completed, the powder bed drops incrementally and a roller or blade smoothens the powder over the surface of the bed, prior to the next pass of the jet heads, with the binder for the subsequent layer to be formed and fused with the previous layer.
Materials: Sandstone powder
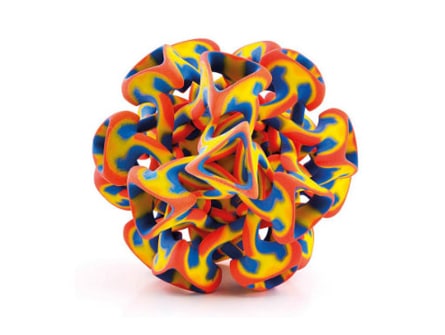
Source: CD3D
MULTI JET FUSION
Multi Jet Fusion is a powder-based technology but does not use lasers. The powder bed is heated uniformly at the outset. A fusing agent is jetted where particles need to be selectively molten, and a detailing agent is jetted around the contours to improve part resolution. While lamps pass over the surface of the powder bed, the jetted material captures the heat and helps distribute it evenly.
Multi Jet Fusion’s unique build style includes fusing and detailing agents within a powder-bed fusion process. The build begins with a thin layer of powdered material being deposited across the build platform. Droplets of fusing, detailing and transforming agents are applied along with thermal energy on top of the powdered material to define the part’s geometry and properties.
The process continues layer-by-layer until a complete part is formed. After the print is finished, the build unit with the material and parts are rolled onto a processing station for cooling and powder excavation.
Materials: Nylon (PA12)
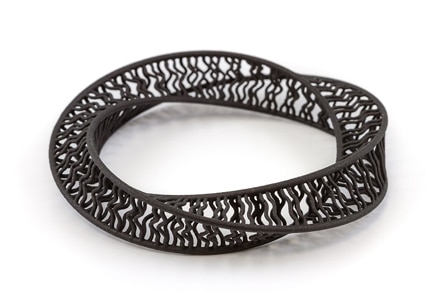
POLY JET PRINTING
PolyJet is a layer additive manufacturing technology used to develop plastic prototypes from 3D CAD data. This rapid prototyping process uses ink-jet technology combined with UV curable materials to quickly and economically produce highly detailed and accurate physical prototypes. PolyJet is one of the fastest prototyping processes available to develop high-precision physical parts, and is ideal for smaller parts appearance models and master pattern.
The PolyJet process begins by slicing CAD data into cross-sections or layers as thin as sixteen-thousands of each. The data is then transferred to the polyjet machine which begins constructing the object one layer at a time from the bottom up. Similar to how an ink-jet printer lays down pigment, the PolyJet print head deposits small amounts of ultraviolet curable material on the build platform. Eventually forming a single cross-section of the part. An ultraviolet light attached to the print head simultaneously cures the material as it is printed. Once a cross section is complete, the build platform is lowered slightly to make room for the next layer. As the part is built, support material is added to give supplemental strength to fine structures and down-facing surfaces. After all of the layers have been created, the finished part is removed from the platform and cleaned.
Materials: Photo polymer resin
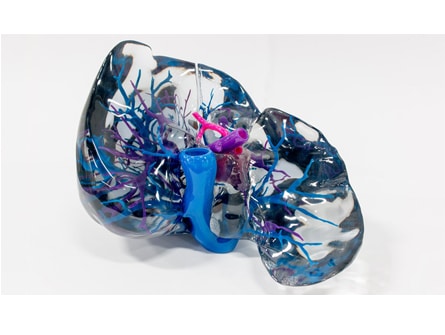
Source: 3Dnatives
MULTI JET PRINTING
MJP is used to build parts, patterns and molds with fine feature detail to address a wide range of applications. These high-resolution printers are economical to own and operate and use a separate, meltable or dissolvable support material to make post-processing a breeze. Another big benefit is that removing support material is virtually a hands-free operation and allows even the most delicate features and complex internal cavities to be thoroughly cleaned without damage.
MJP printers offer the highest Z-direction resolution with layer thicknesses as low as 16 microns. In addition, selectable print modes allow the user to choose the best combination of resolution and print speed, so it’s easy to find a combination that meets your needs. Parts have smooth finish and can achieve accuracies rivaling SLA for many applications. Recent material advances have improved the durability of plastic materials and are now suitable for some end-use applications.
Materials:
- ∗VisiJet® M2R-WT (Rigid White, General Purpose)
- ∗VisiJet® M2R-BK (Rigid Black, General Purpose)
- VisiJet® M2G-DUR (VisiJet ProFlex, PP-like)
- VisiJet® M2R-GRY (Rigid Gray, High Contrast)
- VisiJet® M2G-CL (VisiJet Armor, Clear, ABS-like)
- VisiJet® M2R-CL (Rigid Clear, General Purpose)
- VisiJet® M2-EBK (Elastomeric Black, High Flex)
- VisiJet® M2-ENT (Elastomeric Natural, High Flex)
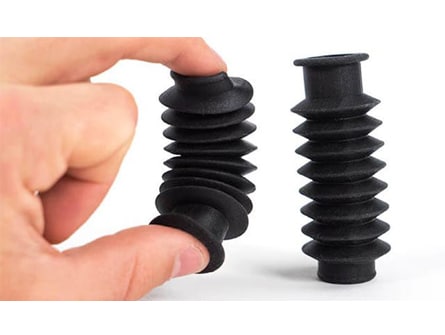
Click here to know more about 3D Printers, 3D Printing services and it’s applications.